GLEN Industries coming with IPO to raise Rs 63 crore
The issue will open on July 8, 2025 and will close on July 10, 2025
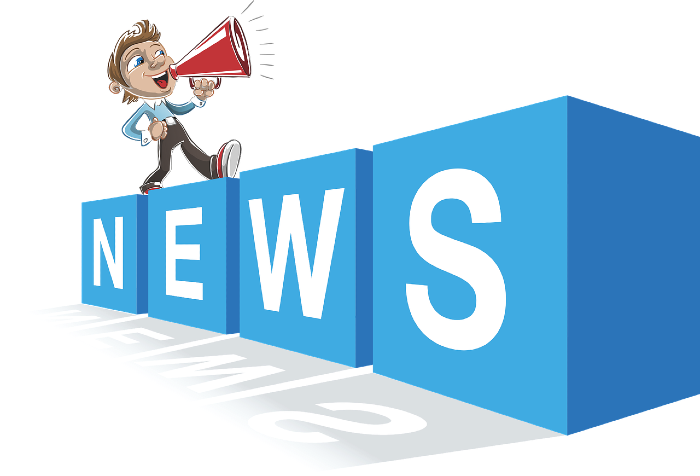
GLEN Industries
- GLEN Industries is coming out with an initial public offering (IPO) of 64,96,800 equity shares in a price band Rs 92-97 per equity share.
- The issue will open on July 8, 2025 and will close on July 10, 2025.
- The shares will be listed on SME Platform of BSE.
- The face value of the share is Rs 10 and is priced 9.20 times of its face value on the lower side and 9.70 times on the higher side.
- Book running lead manager to the issue is GYR Capital Advisors.
- Compliance Officer for the issue is Shikha Sureka.
Profile of the company
GLEN Industries is engaged in the manufacturing of diverse range of Food packaging and Service Products, primarily Thin Wall Food Containers, Polylactic Acid (PLA) Straws and Paper Straws all mainly supplied to the Hotel, Restaurant, and Café/Catering (HoReCa) sector, Beverage industry and food packaging industry. Its extensive product lineup, available in various shapes and sizes, is widely favored by sectors such as the HoReCa industry, Quick Service Restaurants (QSR), the food, beverage and dairy industry, etc.
The company’s product lineup is organized into two primary segments: a diverse range of Thin Wall Food Containers and a comprehensive selection of straws, including both PLA and Paper Straws. This structure allows it to focus on delivering high-quality solutions in each category, catering to the specific needs of its customers. Customization on standardised products can be done by way of digital printing, shrink sleeving, dry offset printing, pad printing & screen printing. Its success is driven by a highly skilled workforce and a dynamic, experienced technical team, ensuring consistent, round-the-clock performance. It maintains strict adherence to international hygiene standards and rigorous quality control measures, which, combined with its ability to meet every buyer's requirement, have enabled it to surpass the competition and earn the trust of its customers. With all operations housed under one roof, it maintains streamlined processes and a cohesive approach to delivering excellence.
Its products are manufactured in strict compliance with FSSC 22000, ISO 9001:2015, Hazard Analysis & Critical Control Point (HACCP) standards. The company is also certified for ISO 14001:2015 for Environment Management System, FSC for Forest Management Certification and SEDEX 4 Pillar for Labour Standards, Health & Safety, Environment and Business Ethics. It uses high-grade raw materials to ensure its products meet both national and international quality benchmarks. Each product undergoes a rigorous quality and testing process before reaching the market, ensuring the highest level of safety and reliability. It has been exporting its products regularly to the Europe, USA, Australia, Middle East and Africa to name a few. Its products are designed, developed and manufactured as per countries local use & preferences. Regular & repeated business from 25+ customers over the years speak volumes of its commitment towards quality & consistency.
Proceed is being used for:
- For setting up a new manufacturing facility at Jaugram, West Bengal
- General corporate purpose
Industry Overview
Plastic packaging is at the center of a new era in the Indian packaging industry. Its versatile usage is becoming the foundation for many industries for product packaging. Compared to other packaging types, plastic packaging containers provide unique benefits, such as high impact strength, stiffness, and barrier properties, which have expanded the market for plastic packaging in recent years. The market for beverage packaging has grown significantly over the last few years in India. Rapid changes in beverage packaging trends across the country are critical for the market's growth. The new trends in the packaging of beverages focus on structural changes, as well as the development of recycled materials like post-consumer recycling, customer acceptance, safety, and new filling technologies. The development of heat-resistant PET bottles improved the preservation of several drinks. The India Plastic Packaging Market size is estimated at $21.77 billion in 2024, and is expected to reach $25.35 billion by 2029, growing at a CAGR of 3.09% during the forecast period (2024-2029).
The food industry's demand for plastic packaging is driven by the need for convenient, compact solutions, particularly with the increasing popularity of ready-to-eat meals. These meals, often packaged in sealed trays of various shapes, including round containers and salad packs, are now seeing a notable shift toward using sustainable and environmentally friendly materials. This strategic move aligns with consumer preferences for eco-conscious packaging solutions, indicating a commitment to meeting market demands and reducing environmental impact within the industry. Flexible packaging comes in various forms, such as pouches, bags, films, and wraps, allowing for versatile packaging solutions to accommodate different cuts, portion sizes, and packaging formats within the meat, poultry, and fish industries. This enables efficient packaging of a wide range of products, from whole cuts to processed items like sausages and fillets.
Furthermore, plastic trays and containers are used in numerous industries as food containers in cafeterias, restaurants, homes, offices, etc. Food services businesses like restaurants utilize food packaging trays for takeout and delivery services, assuring food remains secure and presentable. Besides, other sectors like cafes and bakeries depend on these trays for packaging and displaying their products, improving customer convenience and appeal. The growth of e-commerce in India creates the demand for different food products. The rise of online retail sales in the county grew significantly from $87 million in 2022, and it is forecasted to reach $173 million by 2027. Growing retail online sales show that the demand for food packaging is increasing in India. Moreover, plastic bottles and containers have gained importance in the food industry due to their ability to provide longer shelf life to packaged food items.
Pros and strengths
Advanced in-house processing facilities with focus on cost competitiveness: The company’s modern production facilities are equipped with advanced and modern machineries and adhere to the highest industry standards. It maintains strict hygiene and safety protocols to ensure the integrity of its products at every stage of the manufacturing process. Its investment in advanced manufacturing facilities and cost competitiveness is driven by its commitment to customer satisfaction. It understands that affordability is a key consideration for its customers, and it continuously strives to deliver products that offer exceptional value for money. It prioritizes waste reduction, process optimization, and continuous improvement to eliminate inefficiencies and drive down costs. By minimizing waste and maximizing resource utilization, it ensures that every aspect of its operations adds value to its products without inflating costs.
Quality assurance: The company’s products are manufactured with strict adherence to globally recognized standards, including FSSC 22000, ISO 9001:2015, and Hazard Analysis & Critical Control Point (HACCP) guidelines, ensuring exceptional quality and food safety. Additionally, the company holds ISO 14001:2015 certification for Environmental Management Systems, demonstrating its commitment to sustainable practices, along with FSC certification for responsible forest management and SEDEX 4 Pillar accreditation, covering Labour Standards, Health & Safety, Environmental Responsibility, and Business Ethics. By sourcing high-grade raw materials, it ensures that its products consistently meet both national and international quality benchmarks.
Customization capabilities: It provides customizable designs, sizes, and branding options offering unparalleled flexibility to cater to the diverse and evolving needs of clients, particularly in the food service and retail sectors. This adaptability allows the company to create packaging solutions that align perfectly with their brand identity, enhance product appeal, and meet specific functional requirements. Whether it’s developing containers in unique shapes and sizes to accommodate specialized food items or incorporating logos, colors, and designs that reinforce brand recognition, customization empowers clients to differentiate themselves in competitive markets.
Risks and concerns
Dependent on external suppliers for most of its component requirements and raw materials: The company relies heavily on external suppliers for most of its machinery, components, and raw material needs. Any failure on the part of its suppliers to deliver these materials or components in the required quantities, within the agreed timelines, or in compliance with specified quality standards and technical specifications could negatively impact its operations. Such failures may hinder its ability to deliver products on time and at the desired quality levels, potentially resulting in contractual penalties, liabilities for non-performance, loss of customers, and damage to its reputation. Additionally, identifying and qualifying alternative suppliers who meet its technical and quality standards and can supply the required quantities would involve significant costs and could delay the delivery of its products. These factors could materially and adversely affect its business, financial condition, and operational results.
Depend on its manufacturing facilities in West Bengal: The company conducts its operations through its manufacturing facility situated at Howrah District in West Bengal. The concentration of all of its manufacturing operations in Howrah exposes it to adverse developments related to regulation, as well as political or economic, demographic and other changes in West Bengal as well as the occurrence of natural and man-made disasters in West Bengal, which may adversely affect business, financial condition and results of operations. Its manufacturing operations require significant labour and are also reliant on government policies in terms of taxes, duties and incentives made applicable by the state government. As a result, any unfavorable policies of the state government or state or local governments in this region, could adversely affect its business, financial condition and results of operations.
Significant revenue comes from exports: The company has historically derived a significant portion of its revenue from exporting to other countries. The company has garnered 33.48%, 32.98% and 37.27% of its revenue from exports in FY25, FY24 and FY23 respectively. Therefore, any adverse developments in the global economy or the industries in which its customers operate could have an impact on its sales from exports. From time to time, tariffs, quotas and other tariff and non-tariff trade barriers may be imposed on its products in jurisdictions in which it operates or seek to sell its products. There can be no assurance that the countries where it exports, among others, where it seeks to sell its products will not impose trade restrictions on it in future. It may also be prohibited from exporting to certain restricted countries that may be added to a sanctions list maintained by the Government of India or other foreign governments. Any such imposition of trade barriers may have an adverse effect on its results of operations and financial condition.
Outlook
Glen Industries is engaged in the manufacturing of eco-friendly food packaging and service products. The company specializes in producing thin-wall food containers and compostable straws, serving sectors such as Hotels, Restaurants, Cafes/Catering (HoReCa), the beverage industry, and food packaging. The company has advanced in-house processing facilities with focus on cost competitiveness. On the concern side, the company derives a significant portion of its revenues from exports and are subject to risk of international trade. Moreover, the company is dependent on external suppliers for most of its machinery / component requirements and raw materials.
The company is coming out with a maiden IPO of 64,96,800 equity shares of Rs 10 each. The issue has been offered in a price band of Rs 92-97 per equity share. The aggregate size of the offer is around Rs 59.77 crore to Rs 63.02 crore based on lower and upper price band respectively. On performance front, the company’s revenue from operations of the company for fiscal year 2025 was Rs 17,066.09 lakh against Rs 14,450.02 lakh for Fiscal year 2024, an increase of 18.10% in revenue from operations. The increase in revenue was primarily driven by a rise in the overall production of TWC and Straws, which in turn resulted in higher sales. Moreover, profit after tax for the Fiscal year 2025 was at Rs 1,826.57 lakh against profit after tax of Rs 857.89 lakh in fiscal year 2024, an increase of 112.91%.
The company intends to continue to invest in technology infrastructure to enable further technical innovation, improve its operational efficiencies, increase customer satisfaction and improve its sales and profitability. It intends to continue to focus on optimizing and automating its manufacturing processes to improve returns in a rapidly changing technological environment. It is proposing to utilize Rs 4773.00 lakh towards expansion of its manufacturing capabilities. Further, by expanding its technological capabilities it intends to be more cost-efficient player in each of the products it manufactures. Economies of scale will also enable it to continuously improve its operational efficiencies. It will continue with this strategy of invest in expanding its technological capabilities and manufacturing capacities which will also help it in attaining cost efficiency.